Introduction
The ceramics industry is vast, and it touches nearly every aspect of our daily lives. From fine china to industrial ceramics, the materials used to produce these items must be both durable and precise. One material that has gained significant attention in recent years is fused alumina. Fused alumina, a high-performance ceramic material, is valued for its hardness, strength, and thermal stability, making it an ideal component in ceramic production. But how does fused alumina contribute to the production process, and what role does it play in creating products that stand the test of time?
In this article, we will explore the role of fused alumina in ceramic production, examine real-world examples of its applications, and hear from industry experts about why it has become indispensable in modern ceramics manufacturing.
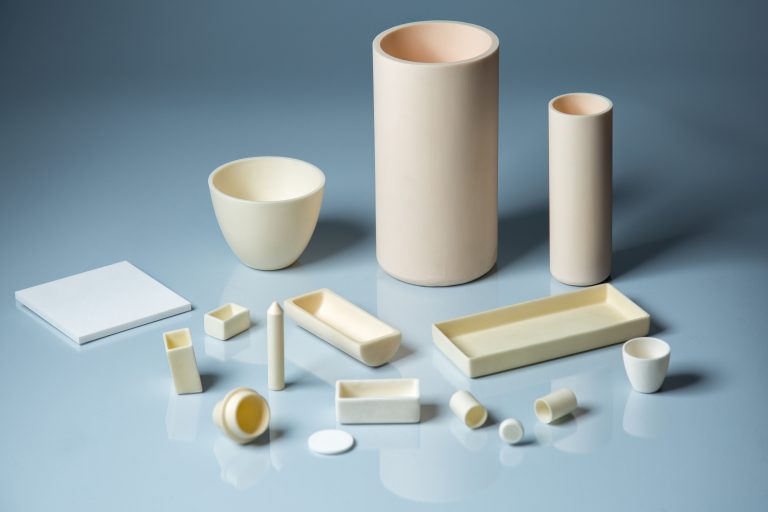
The Role of Fused Alumina in Ceramic Production
Fused alumina, also known as corundum, is a high-purity form of aluminum oxide (Al₂O₃) produced by melting alumina at extremely high temperatures. It is characterized by its hardness, high melting point, and chemical stability, which makes it invaluable in various ceramic applications. In the ceramic industry, fused alumina is used primarily as an abrasive material, a component in refractory products, and as a stabilizing agent in certain types of glazes.
When added to ceramic products, fused alumina enhances the product’s ability to withstand extreme temperatures and physical wear. This is particularly useful in industries where high-performance materials are required, such as in the production of industrial tiles, refractory linings, and advanced ceramic components used in aerospace and electronics.
Example: In the production of high-temperature ceramic linings for furnaces, fused alumina is often used to improve the resistance of the material to both heat and wear. This allows manufacturers to create linings that can endure harsh environments and extend the lifespan of equipment significantly.
Real-World Applications of Fused Alumina in Ceramic Production
To fully appreciate the impact of fused alumina in ceramic production, let’s explore some actual cases where it has transformed the manufacturing process and product quality.
1. Industrial Tiles and Flooring
Fused alumina is commonly used in the production of industrial tiles and flooring materials. These products are often subjected to heavy loads, abrasion, and chemical exposure, especially in factories, laboratories, and kitchens. Fused alumina provides the necessary hardness and durability to withstand such conditions.
Case Study: A leading manufacturer of industrial flooring reported a significant increase in the durability of their products after switching to fused alumina-based compositions. The company noted a 40% reduction in wear and tear, which translated into longer-lasting flooring and reduced maintenance costs.
2. Refractory Materials
In the production of refractory materials, such as kiln linings and crucibles, fused alumina plays a critical role in enhancing the heat resistance and stability of the final product. These materials are essential in industries such as steel production, glass manufacturing, and ceramics.
Success Story: A ceramic manufacturer specializing in high-performance crucibles for the aerospace industry adopted fused alumina in their products. The result was a marked improvement in thermal conductivity and resistance to thermal shock, which allowed their customers to achieve more efficient and cost-effective manufacturing processes.
3. Glazes and Coatings
Fused alumina is also used in ceramic glazes and coatings to improve their aesthetic quality and functional properties. It is often incorporated into high-quality porcelain, where it enhances the glaze’s ability to resist scratching, staining, and chemical damage.
User Feedback: Many ceramic artists and manufacturers have reported a noticeable improvement in the durability and appearance of their glazed products after incorporating fused alumina. One artist specializing in luxury porcelain dinnerware found that fused alumina provided a finer, more polished finish, while also making the pieces resistant to everyday use and wear.
Expert Insights on the Benefits of Fused Alumina in Ceramic Production
Industry experts have long recognized the value of fused alumina in ceramic production. According to Dr. John Hartman, a leading researcher in materials science, “Fused alumina’s unique properties—especially its hardness and thermal stability—make it an ideal additive in many ceramic formulations, from industrial components to consumer goods.”
Further supporting this view, a study published by the Journal of Ceramic Engineering highlights that the use of fused alumina in advanced ceramic components can result in up to a 30% increase in thermal shock resistance, making it a crucial material for industries that rely on high-performance ceramics.
Moreover, with the global push towards more sustainable manufacturing practices, fused alumina is becoming increasingly popular due to its non-toxic nature and its ability to enhance the longevity of ceramic products. This, in turn, reduces waste and the frequency of product replacement.
Why Fused Alumina Matters for Your Ceramic Production Needs
As we’ve seen from the various case studies and expert insights, fused alumina is an invaluable material in the ceramics industry. Whether you're producing industrial tiles, refractory products, or fine porcelain, fused alumina offers the perfect balance of strength, durability, and thermal stability. By incorporating fused alumina into your production process, you can improve the overall quality and lifespan of your products, which translates into reduced operational costs and better performance.
If you are looking to enhance your ceramic products or explore new possibilities in manufacturing, fused alumina could be the key to unlocking greater potential. Many industry leaders, such as Henan Sanhui New Materials Co., Ltd., offer high-quality fused alumina to meet the specific needs of ceramic manufacturers.
Conclusion
Fused alumina is not just a material—it's a game changer in ceramic production. From improving product durability to enhancing aesthetic qualities, it plays a vital role in helping manufacturers achieve high-performance results. With its proven track record in various applications, fused alumina continues to drive innovation in the ceramics industry. If you’re looking to stay ahead of the competition and produce top-tier ceramic products, investing in fused alumina is a decision that can deliver tangible results.