Introduction
Fused alumina, a highly durable and heat-resistant material, is a crucial component in many industrial applications. It is used in abrasives, refractories, and advanced ceramics due to its extreme hardness and thermal stability. But how is it made? Understanding the fused alumina production process not only sheds light on its manufacturing complexities but also highlights why it is so valued across industries.
In this blog, we will explore the step-by-step production of fused alumina, discuss real-world applications, and hear insights from industry experts on why it remains the gold standard for high-performance materials.
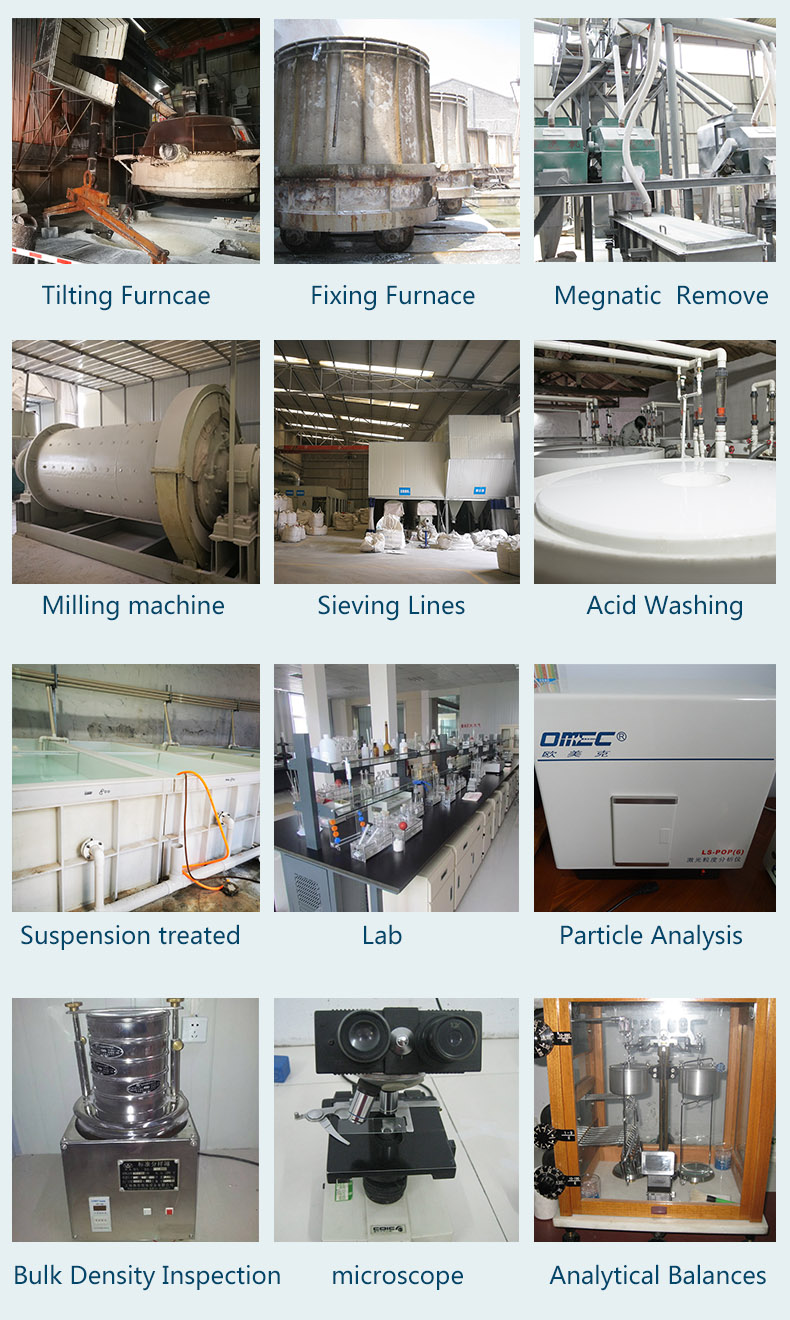
The Fused Alumina Production Process
1. Raw Material Selection: The Foundation of Quality
The production of fused alumina starts with high-purity aluminum oxide (Al₂O₃), commonly sourced from bauxite or synthetic alumina. The quality of these raw materials directly affects the final product's hardness, purity, and thermal stability.
Leading manufacturers use high-grade bauxite or chemically refined alumina to ensure minimal impurities. According to industry expert Dr. Mark Reynolds, “The key to producing superior fused alumina is starting with the purest aluminum oxide. Any contamination can negatively impact its performance in high-precision applications.”
2. Electric Arc Furnace Melting: High-Temperature Transformation
The next step involves melting the aluminum oxide in a high-power electric arc furnace at temperatures exceeding 2,000°C (3,632°F). This extreme heat causes the raw material to liquefy, allowing impurities to separate and burn off.
During this phase, different processing techniques can be used to produce variations such as white fused alumina (high-purity), brown fused alumina (with iron oxide for added toughness), and pink fused alumina (chromium oxide-enhanced for wear resistance).
Case Study: A leading abrasives manufacturer switched to an advanced arc melting process and reported a 15% increase in product uniformity. This improvement led to better performance in grinding applications, significantly reducing tool wear.
3. Controlled Cooling and Crystallization
After melting, the molten alumina is carefully cooled and solidified into large crystal blocks. The cooling rate directly impacts the crystalline structure, affecting properties such as toughness and fracture resistance.
Slow cooling results in larger, more defined crystals, which are preferred in certain high-strength applications. In contrast, rapid cooling produces finer grains, ideal for precision cutting and polishing applications.
4. Crushing and Sizing: Tailoring to Specific Applications
Once solidified, the fused alumina blocks are crushed and processed into different particle sizes. This step is critical because different industries require varying degrees of coarseness or fineness.
For example:
- Coarse grains (12-24 mesh): Used in heavy-duty sandblasting and grinding wheels.
- Medium grains (36-80 mesh): Commonly found in bonded abrasives for precision machining.
- Fine grains (120-600 mesh): Preferred in polishing and lapping applications for achieving ultra-smooth finishes.
5. Purification and Quality Control
To meet industrial standards, the final fused alumina must go through a rigorous purification and testing process. Magnetic separation removes any remaining metallic impurities, while chemical analysis ensures that the product meets the required purity levels.
Success Story: A leading refractory manufacturer implemented a state-of-the-art purification system, reducing contamination levels by 20%. This innovation resulted in stronger and more reliable refractory materials used in steel and glass manufacturing.
Real-World Applications of Fused Alumina
1. Abrasives Industry: Precision Grinding and Polishing
One of the largest consumers of fused alumina is the abrasives industry. Grinding wheels, sandpaper, and cutting tools rely on its hardness to cut through tough materials efficiently.
User Feedback: “Since switching to premium fused alumina abrasives, we’ve seen a 30% improvement in grinding efficiency, with fewer tool replacements needed,” reports a senior engineer from a leading automotive component manufacturer.
2. Refractory Materials: High-Temperature Resistance
Fused alumina is an essential ingredient in refractory bricks, kiln linings, and furnace insulation. Its ability to withstand extreme temperatures without breaking down makes it ideal for steel, glass, and cement manufacturing.
3. Advanced Ceramics: High-Performance Components
Industries such as aerospace and medical implants utilize fused alumina in ceramic coatings and structural components. The material’s exceptional wear resistance ensures long-lasting performance in demanding environments.
Expert Quote: According to Dr. Emily Carter, a ceramic materials scientist, “Fused alumina’s combination of hardness and chemical stability makes it an invaluable material in next-generation ceramic components for aerospace and biomedical applications.”
Why Fused Alumina Matters for Your Industry
Whether you're in manufacturing, engineering, or industrial design, the benefits of fused alumina cannot be overlooked. It enhances productivity, improves product durability, and reduces operational costs.
If you’re looking for a high-quality fused alumina supplier, be sure to choose a manufacturer that prioritizes purity, consistency, and advanced production techniques.
Conclusion
The production of fused alumina is a sophisticated process that transforms raw aluminum oxide into a material of unparalleled industrial value. From high-temperature melting to precise grain sizing, every step ensures that the final product meets the stringent demands of industries ranging from abrasives to advanced ceramics.
With its exceptional hardness, thermal resistance, and chemical stability, fused alumina continues to be a fundamental material in modern manufacturing. Whether you're cutting, grinding, or producing high-performance refractory materials, understanding the fused alumina production process gives you valuable insight into its importance.
For businesses seeking superior fused alumina solutions, partnering with a trusted supplier ensures consistent quality and performance in all applications. As industries evolve, so too does the need for advanced materials—fused alumina is undoubtedly one of them.